Some cool china tooling produce services manufacturers images:
Steven F. Udvar-Hazy Center: SR-71 Blackbird (tail view)
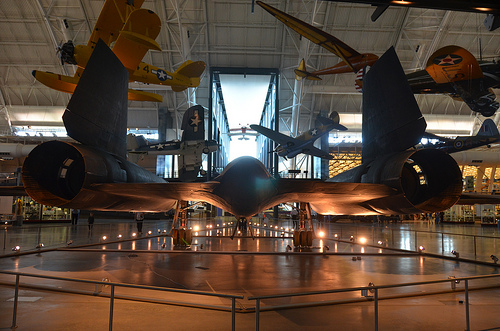
Image by Chris Devers
See more photos of this, and the Wikipedia article.
Details, quoting from Smithsonian National Air and Space Museum | Lockheed SR-71 Blackbird:
No reconnaissance aircraft in history has operated globally in more hostile airspace or with such complete impunity than the SR-71, the world’s fastest jet-propelled aircraft. The Blackbird’s performance and operational achievements placed it at the pinnacle of aviation technology developments during the Cold War.
This Blackbird accrued about 2,800 hours of flight time during 24 years of active service with the U.S. Air Force. On its last flight, March 6, 1990, Lt. Col. Ed Yielding and Lt. Col. Joseph Vida set a speed record by flying from Los Angeles to Washington, D.C., in 1 hour, 4 minutes, and 20 seconds, averaging 3,418 kilometers (2,124 miles) per hour. At the flight’s conclusion, they landed at Washington-Dulles International Airport and turned the airplane over to the Smithsonian.
Transferred from the United States Air Force.
Manufacturer:
Lockheed Aircraft Corporation
Designer:
Clarence L. "Kelly" Johnson
Date:
1964
Country of Origin:
United States of America
Dimensions:
Overall: 18ft 5 15/16in. x 55ft 7in. x 107ft 5in., 169998.5lb. (5.638m x 16.942m x 32.741m, 77110.8kg)
Other: 18ft 5 15/16in. x 107ft 5in. x 55ft 7in. (5.638m x 32.741m x 16.942m)
Materials:
Titanium
Physical Description:
Twin-engine, two-seat, supersonic strategic reconnaissance aircraft; airframe constructed largley of titanium and its alloys; vertical tail fins are constructed of a composite (laminated plastic-type material) to reduce radar cross-section; Pratt and Whitney J58 (JT11D-20B) turbojet engines feature large inlet shock cones.
Long Description:
No reconnaissance aircraft in history has operated in more hostile airspace or with such complete impunity than the SR-71 Blackbird. It is the fastest aircraft propelled by air-breathing engines. The Blackbird’s performance and operational achievements placed it at the pinnacle of aviation technology developments during the Cold War. The airplane was conceived when tensions with communist Eastern Europe reached levels approaching a full-blown crisis in the mid-1950s. U.S. military commanders desperately needed accurate assessments of Soviet worldwide military deployments, particularly near the Iron Curtain. Lockheed Aircraft Corporation’s subsonic U-2 (see NASM collection) reconnaissance aircraft was an able platform but the U. S. Air Force recognized that this relatively slow aircraft was already vulnerable to Soviet interceptors. They also understood that the rapid development of surface-to-air missile systems could put U-2 pilots at grave risk. The danger proved reality when a U-2 was shot down by a surface to air missile over the Soviet Union in 1960.
Lockheed’s first proposal for a new high speed, high altitude, reconnaissance aircraft, to be capable of avoiding interceptors and missiles, centered on a design propelled by liquid hydrogen. This proved to be impracticable because of considerable fuel consumption. Lockheed then reconfigured the design for conventional fuels. This was feasible and the Central Intelligence Agency (CIA), already flying the Lockheed U-2, issued a production contract for an aircraft designated the A-12. Lockheed’s clandestine ‘Skunk Works’ division (headed by the gifted design engineer Clarence L. "Kelly" Johnson) designed the A-12 to cruise at Mach 3.2 and fly well above 18,288 m (60,000 feet). To meet these challenging requirements, Lockheed engineers overcame many daunting technical challenges. Flying more than three times the speed of sound generates 316° C (600° F) temperatures on external aircraft surfaces, which are enough to melt conventional aluminum airframes. The design team chose to make the jet’s external skin of titanium alloy to which shielded the internal aluminum airframe. Two conventional, but very powerful, afterburning turbine engines propelled this remarkable aircraft. These power plants had to operate across a huge speed envelope in flight, from a takeoff speed of 334 kph (207 mph) to more than 3,540 kph (2,200 mph). To prevent supersonic shock waves from moving inside the engine intake causing flameouts, Johnson’s team had to design a complex air intake and bypass system for the engines.
Skunk Works engineers also optimized the A-12 cross-section design to exhibit a low radar profile. Lockheed hoped to achieve this by carefully shaping the airframe to reflect as little transmitted radar energy (radio waves) as possible, and by application of special paint designed to absorb, rather than reflect, those waves. This treatment became one of the first applications of stealth technology, but it never completely met the design goals.
Test pilot Lou Schalk flew the single-seat A-12 on April 24, 1962, after he became airborne accidentally during high-speed taxi trials. The airplane showed great promise but it needed considerable technical refinement before the CIA could fly the first operational sortie on May 31, 1967 – a surveillance flight over North Vietnam. A-12s, flown by CIA pilots, operated as part of the Air Force’s 1129th Special Activities Squadron under the "Oxcart" program. While Lockheed continued to refine the A-12, the U. S. Air Force ordered an interceptor version of the aircraft designated the YF-12A. The Skunk Works, however, proposed a "specific mission" version configured to conduct post-nuclear strike reconnaissance. This system evolved into the USAF’s familiar SR-71.
Lockheed built fifteen A-12s, including a special two-seat trainer version. Two A-12s were modified to carry a special reconnaissance drone, designated D-21. The modified A-12s were redesignated M-21s. These were designed to take off with the D-21 drone, powered by a Marquart ramjet engine mounted on a pylon between the rudders. The M-21 then hauled the drone aloft and launched it at speeds high enough to ignite the drone’s ramjet motor. Lockheed also built three YF-12As but this type never went into production. Two of the YF-12As crashed during testing. Only one survives and is on display at the USAF Museum in Dayton, Ohio. The aft section of one of the "written off" YF-12As which was later used along with an SR-71A static test airframe to manufacture the sole SR-71C trainer. One SR-71 was lent to NASA and designated YF-12C. Including the SR-71C and two SR-71B pilot trainers, Lockheed constructed thirty-two Blackbirds. The first SR-71 flew on December 22, 1964. Because of extreme operational costs, military strategists decided that the more capable USAF SR-71s should replace the CIA’s A-12s. These were retired in 1968 after only one year of operational missions, mostly over southeast Asia. The Air Force’s 1st Strategic Reconnaissance Squadron (part of the 9th Strategic Reconnaissance Wing) took over the missions, flying the SR-71 beginning in the spring of 1968.
After the Air Force began to operate the SR-71, it acquired the official name Blackbird– for the special black paint that covered the airplane. This paint was formulated to absorb radar signals, to radiate some of the tremendous airframe heat generated by air friction, and to camouflage the aircraft against the dark sky at high altitudes.
Experience gained from the A-12 program convinced the Air Force that flying the SR-71 safely required two crew members, a pilot and a Reconnaissance Systems Officer (RSO). The RSO operated with the wide array of monitoring and defensive systems installed on the airplane. This equipment included a sophisticated Electronic Counter Measures (ECM) system that could jam most acquisition and targeting radar. In addition to an array of advanced, high-resolution cameras, the aircraft could also carry equipment designed to record the strength, frequency, and wavelength of signals emitted by communications and sensor devices such as radar. The SR-71 was designed to fly deep into hostile territory, avoiding interception with its tremendous speed and high altitude. It could operate safely at a maximum speed of Mach 3.3 at an altitude more than sixteen miles, or 25,908 m (85,000 ft), above the earth. The crew had to wear pressure suits similar to those worn by astronauts. These suits were required to protect the crew in the event of sudden cabin pressure loss while at operating altitudes.
To climb and cruise at supersonic speeds, the Blackbird’s Pratt & Whitney J-58 engines were designed to operate continuously in afterburner. While this would appear to dictate high fuel flows, the Blackbird actually achieved its best "gas mileage," in terms of air nautical miles per pound of fuel burned, during the Mach 3+ cruise. A typical Blackbird reconnaissance flight might require several aerial refueling operations from an airborne tanker. Each time the SR-71 refueled, the crew had to descend to the tanker’s altitude, usually about 6,000 m to 9,000 m (20,000 to 30,000 ft), and slow the airplane to subsonic speeds. As velocity decreased, so did frictional heat. This cooling effect caused the aircraft’s skin panels to shrink considerably, and those covering the fuel tanks contracted so much that fuel leaked, forming a distinctive vapor trail as the tanker topped off the Blackbird. As soon as the tanks were filled, the jet’s crew disconnected from the tanker, relit the afterburners, and again climbed to high altitude.
Air Force pilots flew the SR-71 from Kadena AB, Japan, throughout its operational career but other bases hosted Blackbird operations, too. The 9th SRW occasionally deployed from Beale AFB, California, to other locations to carryout operational missions. Cuban missions were flown directly from Beale. The SR-71 did not begin to operate in Europe until 1974, and then only temporarily. In 1982, when the U.S. Air Force based two aircraft at Royal Air Force Base Mildenhall to fly monitoring mission in Eastern Europe.
When the SR-71 became operational, orbiting reconnaissance satellites had already replaced manned aircraft to gather intelligence from sites deep within Soviet territory. Satellites could not cover every geopolitical hotspot so the Blackbird remained a vital tool for global intelligence gathering. On many occasions, pilots and RSOs flying the SR-71 provided information that proved vital in formulating successful U. S. foreign policy. Blackbird crews provided important intelligence about the 1973 Yom Kippur War, the Israeli invasion of Lebanon and its aftermath, and pre- and post-strike imagery of the 1986 raid conducted by American air forces on Libya. In 1987, Kadena-based SR-71 crews flew a number of missions over the Persian Gulf, revealing Iranian Silkworm missile batteries that threatened commercial shipping and American escort vessels.
As the performance of space-based surveillance systems grew, along with the effectiveness of ground-based air defense networks, the Air Force started to lose enthusiasm for the expensive program and the 9th SRW ceased SR-71 operations in January 1990. Despite protests by military leaders, Congress revived the program in 1995. Continued wrangling over operating budgets, however, soon led to final termination. The National Aeronautics and Space Administration retained two SR-71As and the one SR-71B for high-speed research projects and flew these airplanes until 1999.
On March 6, 1990, the service career of one Lockheed SR-71A Blackbird ended with a record-setting flight. This special airplane bore Air Force serial number 64-17972. Lt. Col. Ed Yeilding and his RSO, Lieutenant Colonel Joseph Vida, flew this aircraft from Los Angeles to Washington D.C. in 1 hour, 4 minutes, and 20 seconds, averaging a speed of 3,418 kph (2,124 mph). At the conclusion of the flight, ‘972 landed at Dulles International Airport and taxied into the custody of the Smithsonian’s National Air and Space Museum. At that time, Lt. Col. Vida had logged 1,392.7 hours of flight time in Blackbirds, more than that of any other crewman.
This particular SR-71 was also flown by Tom Alison, a former National Air and Space Museum’s Chief of Collections Management. Flying with Detachment 1 at Kadena Air Force Base, Okinawa, Alison logged more than a dozen ‘972 operational sorties. The aircraft spent twenty-four years in active Air Force service and accrued a total of 2,801.1 hours of flight time.
Wingspan: 55’7"
Length: 107’5"
Height: 18’6"
Weight: 170,000 Lbs
Reference and Further Reading:
Crickmore, Paul F. Lockheed SR-71: The Secret Missions Exposed. Oxford: Osprey Publishing, 1996.
Francillon, Rene J. Lockheed Aircraft Since 1913. Annapolis, Md.: Naval Institute Press, 1987.
Johnson, Clarence L. Kelly: More Than My Share of It All. Washington D.C.: Smithsonian Institution Press, 1985.
Miller, Jay. Lockheed Martin’s Skunk Works. Leicester, U.K.: Midland Counties Publishing Ltd., 1995.
Lockheed SR-71 Blackbird curatorial file, Aeronautics Division, National Air and Space Museum.
DAD, 11-11-01